Oil and gas facility owners and operators are no strangers to addressing tough challenges head-on. Ironing out supply chain wrinkles, meeting the demand for perfection in equipment reliability, never taking an eye off of safety measures, and complying with increasingly stringent regulations are all in a day’s work.
As per- and polyfluoroalkyl substances (PFAS) concerns move toward center stage, the oil and gas industry is poised to assess and address PFAS challenges efficiently and cost-effectively to continue to produce quality products for their markets.
PFAS present unique challenges for oil and gas facilities. Their chemical makeup, the way they move within the environment, the learning curve for sampling and remediation, and the mounting regulatory requirements all make managing PFAS a formidable task.
With the right mix of technical understanding and process engineering, PFAS at impacted oil and gas sites can be well managed. Let’s dive in.
You’ve Detected (or Suspect) PFAS at Your Site. How Did it Get There?
If you’ve detected PFAS at your site or suspect PFAS may be present, you might be curious to understand how it got there. Like many things PFAS, the answer is often complex, but previous aqueous film-forming foam (AFFF) storage or use for firefighting events or training may be a source.
The very properties that make PFAS a challenge to remediate make it a great firefighter. Beginning in 1965, United States military specifications required PFAS in firefighting foams, and PFAS-containing foams (specifically, AFFF) became an industry standard for extinguishing Class B (flammable liquid) fires.
In addition to traveling onsite through AFFF, PFAS are widely used by industry and in consumer products. Everyday products associated with PFAS include non-stick coatings, water-repellent surfaces, stain-repellant fabrics, and food wrappers. PFAS are also used in electroplating, semiconductor, paper and textile, aerospace, and other industries. Its widespread use makes it hard to know with certainty how PFAS found its way to your site.
AFFF: A source of PFAS
PFAS are an emerging contaminant class that is widely associated with use in flammable liquid (Class-B) firefighting foams, often referred to as AFFF. Historically, AFFF served as one of the best tools for fire management at oil and gas facilities. The current regulatory environment continues to unwrap the extent to which storing and using AFFF has impacted soils and groundwater.
PFAS composition in AFFF has changed over multiple decades, with different manufacturers using different production processes and environmental impacts driving changes to formulations. Even modern Class-B firefighting foams, unless specified as being fluorine-free, are likely to contain PFAS. Present-day AFFF formulations have transitioned to ‘C6’ formulations, consisting of short-chain PFAS and little to no PFOA or PFOS.
How PFAS Travels through Sites
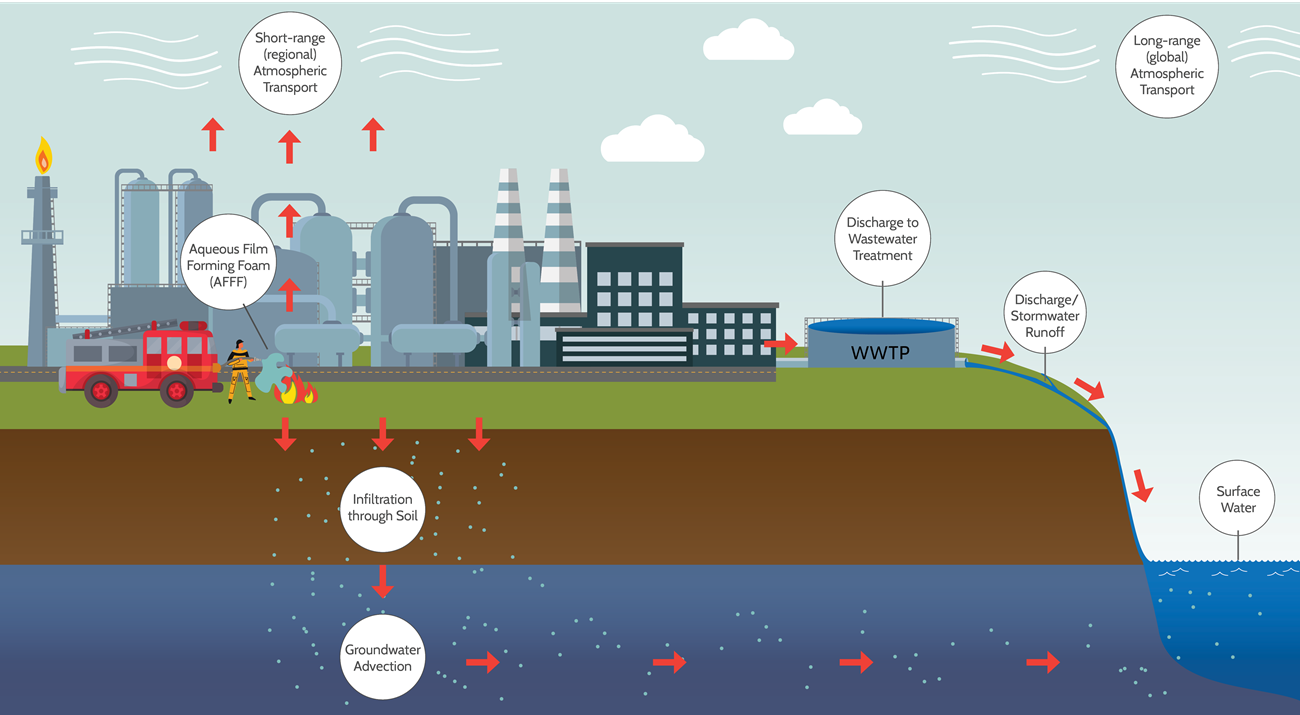
PFAS Regulations Arrive: An Evolving Roadmap
With increasing PFAS detection comes increasing PFAS regulation. A bevy of state and federal requirements have been proposed to manage PFAS impacts, and two regulatory considerations may be of particular interest to oil and gas facility owners and operators:
MCLs
In October 2021, the Environmental Protection Agency (EPA) released a PFAS Strategic Road Map to establish maximum contaminant levels (MCLs) for two PFAS compounds: perfluorooctanoic acid (PFOA) and perfluorooctane sulfonic acid (PFOS). The schedule in the PFAS Strategic Road Map indicates MCLs may be published in 2023 or 2024. The PFAS Strategic Road Map also includes plans to evaluate other PFAS compounds, which may lead to additional MCLs.
Although specific MCL values cannot be predicted, the EPA has published non-enforceable Health Advisory levels of 70 parts per trillion (ppt) for PFOA and PFOS. The EPA has also begun evaluating additional PFAS for MCLs, which may be published further in the future. In addition, at least 27 states have also passed PFAS-related legislation addressing PFAS regulation, remediation, and/or monitoring.
What MCLs mean for oil and gas facilities: MCLs would trigger site characterization and remediation needs at many facilities across the country, including states where PFAS remain unregulated.
CERCLA/RCRA Designation
The EPA is evaluating whether to label PFAS as hazardous substances/hazardous waste under the Comprehensive Environmental Response, Compensation, and Liability Act (CERCLA) or the Resource Conservation and Recovery Act (RCRA), respectively.
What a hazardous designation means for oil and gas facilities: EPA is currently evaluating regulating PFAS as either a CERCLA (Superfund) “Hazardous Substance” or as a RCRA “Hazardous Waste”. In terms of potential PFAS regulations, the path forward for either of these has unprecedented components. Key implications of designating PFAS as a CERCLA hazardous substance include liability considerations and release reporting. Key implications of designating PFAS as a RCRA hazardous waste include “cradle to grave” waste management considerations.
You’ve Received a PFAS Sampling Order. Now What?
Multiple states have begun issuing orders to sample for PFAS in groundwater, surface water, National Pollutant Discharge Elimination System (NPDES) permitted discharge, or other media types. For example, California released a PFAS Phased Investigation Approach in March 2019, followed by a general order for PFAS investigation at refineries and bulk fuel storage terminals in March 2021. As more states begin to investigate potential PFAS sources, oil and gas facility owners and operators may reasonably expect to receive PFAS regulatory orders, if not seen already.
PFAS sampling orders generally require performing a preliminary evaluation of potential PFAS source areas based on known historical AFFF storage, training, or incident response, and you are generally required to sample water upgradient and downgradient of those areas.
With PFAS sampling orders, responding well is often a result of preparing well. If you anticipate a state-issued sampling order, proactively accumulating information on historical AFFF storage can lead to a more efficient/effective response.
PFAS Sampling: 3 Tips for Success
PFAS sampling is notoriously finicky, with a greater risk of sample contamination, if not done correctly, due to their presence in many everyday materials and extremely low levels of interest. PFAS sampling results also come with a high likelihood of scrutiny, with PFAS in drinking water regularly becoming front-page news. PFAS-specific sampling procedures have been developed to reduce or eliminate sample contamination risks and help ensure confidence in sampling results.
Key considerations for PFAS sampling include:
- Careful planning: Before you begin PFAS groundwater sampling, reference state sampling guidelines, where available. Guidelines vary but typically address recommended and/or required sampling equipment, sampling containers, personal protective equipment, field clothing, sampling procedures, and other considerations.
- PFAS-compatible equipment/materials: PFAS is found in all sorts of products, including common sampling materials. For accurate PFAS sampling results, it’s important to confirm that your sampling gear is PFAS-free. It’s also important to change your gloves frequently as this helps reduce the chance that samples be contaminated by touching a material that contains PFAS.
- Allocating adequate time to avoid rushing: PFAS often has low (single-digit ppt) concentrations of interest. Taking your time during sampling helps you obtain quality samples. Not rushing also reduces the risk of compromising a sample by contacting another material.
Site Management: PFAS and AFFF
PFAS management can happen above and below the ground surface.
Above-ground PFAS Site Management: Include AFFF management in incident response planning to reduce long-term liability and uncertainty.
Although AFFF formulations have changed over time to minimize PFOS and PFOA, PFAS may still be present in modern foams unless they are specifically labeled as fluorine-free.. Modern ‘C6’ foam does not contain PFOA or PFOS, but may contain other PFAS compounds. It is important to inventory which parts of your facility have experienced firefighting foam exposure, including storage and transport areas.
When a fire-related incident occurs, extinguishing the fire is the priority and firefighting foams may be needed to minimize property damage and, potentially, to save lives. Once incident response is complete, recovering foam before it can seep into the ground or discharge offsite can reduce environmental impacts of PFAS.
Below-ground PFAS Site Management: Identify the extent of PFAS contamination to prepare for risk mitigation and/or remediation.
Site assessment and characterization can help identify the extent and severity of impacts to subsurface soils and groundwater from historical PFAS releases. If you confirm PFAS contamination exists at a level of concern, risk mitigation and/or remediation may be needed.
Remediating PFAS has proven challenging due to its high solubility and persistence. Nevertheless, currently available PFAS remediation options, while limited, can generally be effective at containment, source isolation, or otherwise limiting future migration potential. PFAS remediation technologies are also continuously improving as considerable investments pour into PFAS remediation research and development.
When managing water streams impacted with PFAS, whether process-related wastewater or extracted groundwater (e.g., through pump-and-treat), conventional water treatment has little to no impact on PFAS removal. Due to the high aqueous solubility and extreme persistence, PFAS are expected to pass through conventional water treatment systems. PFAS may be removed using processes such as granular activated carbon, ion exchange, and a few other treatment technologies, but such systems must be designed and implemented with PFAS in mind to be effective. Most PFAS treatment technologies can be effective in terms of mass removal from water streams, but do not destroy the molecules. Ultimate waste disposal must be considered.
Additional PFAS Considerations for Oil & Gas Facilities
As the technological, scientific, and regulatory landscapes surrounding PFAS management continue to take shape, the following PFAS-related subjects are also gaining attention:
- Fingerprinting/forensics and PFAS source tracking: Additional tools are becoming available to help oil and gas facilities understand how PFAS arrived onsite.
- Current regulatory framework/Toxic Release Inventory (TRI) reporting: The EPA’s recently released PFAS Roadmap provides a path forward for PFAS regulations on several fronts.
- PFAS transport in air: More is becoming understood about PFAS as a potential source of background contamination and/or vapor intrusion, and associated sampling technologies are being developed.
- PFAS disposal and destruction: Current options include landfills, incineration, or deep-well injection; with significant research occurring in this area, advancements and additional options can be expected.
Want to Learn More? Connect with Us!
If you have PFAS management questions, or would like to learn more about how the latest PFAS-related topics may affect your facility and operations, connect with us!
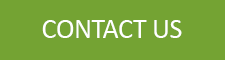
If you'd like a print copy of this article, click here!